SPECIAL SYSTEMS
SITEC SPECIAL SYSTEMS Very careful to customers’ needs and spurred by an always more demanding market, SITEC is very sensible to efficiency and it’s always looking for innovative technologies and the best quality details. Since some years SITEC has been enlarging its production on robotics for a very flexible use, manufactured in few numbers. On its modern plant, SITEC operates with a carefully selected workforce made up of skilled technicians, who provide excellent guarantee of a very high quality standard and an advanced level of technology in continuous development and evolution. With great experience in the various phases making up the welding process, the company is in a position to offer its customers close collaboration aimed at obtaining the best possible solution for the production of just any type of item.

Two-station robotic welding cell for plasma cutting and MIG welding of accessories (pipes, chip pipes…) on bottoms, for tanks of diameters between300 mm and 1250 mm, thickness from 1,5 mm to 5 mm. The equipment is composed of: two robots, one only for welding and the other for plasma cutting and for the positioning of the particular to be welded; of a two-station rotary table with support for the bottom and of a store for the particulars to be welded.



Equipment for single bell-shaping of stainless steel tubes for chimneys, diameters between 80 mm and 350 mm, thickness 0,4-0,6 mm. The unit is equipped with a hydraulic expansion system with 3 inner sectors and 12 outer sectors, shaped and interchangeable for different diameters and for the option male-female.



Automatic equipment for double bell-shaping of stainless steel tubes for chimneys, diameters between 80 mm and 400 mm, thickness 0,4-0,6 mm. The machine is equipped with two units for bell-shaping on an automatic line for chimneys production. On every station there’s a hydraulic expansion system with 3 inner sectors and 12 outer sectors, shaped and interchangeable for different diameters. One station is dedicated to male shaping, while the other is dedicated to female shaping.



This equipment is for bell-shaping of iron tubes for pellet, diameters between 120mm and 250mm, thickness 1,5-2 mm. The unit is equipped with a hydraulic expansion system where there are 8 interchangeable shaped sectors for different diameters.



Standard equipments for longitudinal welding of tubes and sheets with different welding process: Tig, Plasma, Laser, Mig-Mag and Submerged Arc. They are equipped with a copper support resisting to wear and tear and heat and with a series of pressing plates in brass alloy that lock the pieces. Pieces with thickness from 0.5 up to 10 mm and lengths which may go from 30 to 3000 mm are joined together thanks to the sturdiness and high precision of the mechanical processing. The BSL STANDARD series is equipped with a supporting rod in copper settled a fixed height from the ground and it may have a lifting unit being operated by rollers to facilitate preliminary closure and loading/unloading of the pieces.

Liftable equipments for longitudinal welding of tubes and sheets with different welding process: Tig, Plasma, Laser, Mig-Mag and Submerged Arc. They are equipped with a copper support resisting to wear and tear and heat and with a series of pressing plates in brass alloy that lock the pieces. Pieces with thickness from 0.5 up to 10 mm and lengths which may go from 30 to 3000 mm are joined together thanks to the sturdiness and high precision of the mechanical processing. In BSL LIFTABLE series the supporting rod in copper and the bar holding the external pressing plate can move vertically to adjust the unit according to the diameter of the tube to weld. In the lower part of the machine there’s a set of rollers to ensure smooth closure of pipes’ edges and loading/unloading of the pieces.


Automatic equipments for longitudinal welding of tubes and sheets with different welding process: Tig, Plasma, Laser, Mig-Mag and Submerged Arc. They are equipped with a copper support resisting to wear and tear and heat and with a series of pressing plates in brass alloy that lock the pieces. Pieces with thickness from 0.5 up to 4 mm and lengths which may go from 200 to 3000 mm are joined together thanks to the sturdiness and high precision of the mechanical processing. The AUTOMATIC BSL series is suitable for welding pipes by an automatic process of locking the edges of the piece. An adapting cradle, moved by pneumatic or motorized motion, locks the tube aligning the edges and obtaining a very good repetitiveness in big lots of production.

Automatic line for welding and calendering of stainless steel tube of a maximum length of 700 mm and with a diameter ranging between 90 and 150 mm. This equipment includes automatic interlocking of the calender, pick-up unit for the calendered piece and introduction of the welding equipment where operations of gauging, alignment of the tube and TIG longitudinal welding take place. Once the welding phase has been completed, the piece is unloaded on a special slide while another calendered piece is simultaneously introduced into the welding equipment in order to reduce idle time to a minimum and thus increase production output.



Automatic line for bending and welding of stainless steel pipes, maximum length of 1000mm and diameters between 130mm and 240mm. The equipment is composed of: an automatic interlocking bench of the bending unit with an identification system of sheet length, allowing the selfadjustment of the equipment; a two-roll bending unit; a pick-up unit to take the piece to the welding area; a longitudinal welding seamer where operations of gauging, alignment of the tube and plasma welding take place; an automatic unloading bench.



Equipments for inside longitudinal welding of tubes and sheets with different welding process: Tig, Plasma, Laser, Mig-Mag and Submerged Arc. They are equipped with a copper support resisting to wear and tear and heat and with a series of pressing plates in brass alloy that lock the pieces. Pieces with thickness from 0.5 up to 10 mm and lengths which may go from 30 to 8000 mm are joined together thanks to the sturdiness and high precision of the mechanical processing. The BSL series for INSIDE WELDING is suitable for inside welding The BSL series for inside welding is suitable for inside welding of large tubes or sheet metal as its main bar and the torch unit are positioned inside the tube.


Double-lathe automatic equipment for MIG welding of expansion tanks with edge, capacity 24 litres. The unit includes two stations, one for MIG welding of two expansion tanks simultaneously and the other for brushing the welding seam of two expansion tanks simultaneously. On the loading area there’s an automatic loader collecting the expansion tanks.



Expander system for MIG welding of bottoms on tanks of diameters between 1200 mm and 2000 mm, thickness from 2 mm to 5 mm and maximum length of 5mt. The line is composed of a trailer-mounted structure, a fixed expander and a moving beam with an expander at its extremity in order to work different sizes of tanks. The machine is equipped with two expanders complete with a hydraulic system locking the bottom at the tank.



Internal expansion equipment by external circumference welding catering for diameters ranging between 200mm and 1100mm and thicknesses between 0.5 and 3mm of pressed bottoms on stainless steel tubes using a TIG procedure. The basic operation consists in locking both the bottom and the tube being used on a special copper expander which adheres all around the circumference. In this phase, while the pieces are properly locked in position and gauged to adapt to the nominal diameter, they are made to rotate and the circumference welding takes place. Once the welding has been completed, the welding head rotates to facilitate unloading and release of the finished piece after the centre has withdrawn.



Automatic line machine for scaffolding trampling panels spot-welding. Versatility, accuracy and productivity are the main features of this machine.



Two-station robotic welding cell for MIG welding of pre-tacked structures. The unit is equipped with a welding robot and a tilt-rotated positioner on which two pneumatic devices are placed; their function is to lock and centre the non pre-tacked particulars that must be welded to the pre-tacked structure.



This equipment is for circumference welding of curved bottoms and large tubes by means of a SUBMERGED ARC procedure. It is made up of a base with a linear motion system for translation of the Cartesian manipulator over a length of 18000 mm. The front part of the aluminium bar has a submerged arc torch able to rotate to adjust to the piece to be welded. This rotation movement is effected by two pairs of 20000kg motor-run rollers which may work on the same piece on an electrical axis and also individually, which makes it possible to obtain two working stations. The proper positioning of the submerged arc torch on the welding joint is made possible by an electronic proportional probe of our production and a small colour video camera.



Equipment with inclinable lathe for copper-steel and copper-copper brazing of pieces with 200mm and 400mm diameters. This equipment is used for circumference welding of air spaces inside condensation boilers and is equipped with a pneumatic self-centring fixing spindle of our construction and with a mechanical feeler for proper positioning of the torch over the area where welding is to take place.



Equipment with tilting lathe, heavy series, for MIG welding of flanges on steel tubes with a maximum diameter of 600 mm and of a maximum length of 800 mm. The unit is composed of a fixed base and a tilting beam with hydraulic system, of a pneumatic mandrel to lock the tube and its rotation and of a moving tailstock. The torch is moved by two Cartesian axes placed besides the beam.



This is an equipment for the flat welding of iron section bars using the process in submerged arc Twin Arc. The manipulator is mounted on rails and a receding beam reduces the overall dimensions on the rear area during the welding. By the technology Twin Arc it’s possible to make the maximum use of the equipment reaching high welding speeds and very good seams. The machine is equipped with a proportional electronic sewing probe.



Innovative equipment for the assembly and welding of curved bottoms onto tubes of different lengths and diameters. Like all the equipment produced by Sitec, this is equipped with numerical control for convenient management of the axes which configure the system according to the piece being processed: rotation speed, height of torch and length of tube. By oil-dynamic shifting of both lateral carriages and of the centring plates, this equipment may be used for welding operations on pieces by head-to-head joining as well as bordering between bottom and tube. The diameters admitted may vary from 500 to 1250 mm while lengths range between 1200 and 3000 mm. The processing cycle takes place as follows:
• Loading of bottoms by special loading units on both heads and insertion of the tube on the lifting unit placed in the centre of the equipment.
• Assembly of bottoms and tubes by means of the advancement of the heads and by using 48 centring plates.
• Withdrawal of centring plates and simultaneous lowering of both torches for Mig welding.
• Opening of the spindle heads and unloading of tank onto rear rollers.
For head-to-head fitting, a stitching phase takes place between the various centring plates before these are released.



Equipment for MIG welding of coupling sleeves on iron cylinders, diameters between 32 mm and 160 mm and maximum length of 1200 mm. The unit is made up of a partially closed structure with manually opening doors, of a supporting column for rotary welding system and of a bearing device to lock and centre the particular to weld.



This is an equipment for MIG welding of coupling sleeves on iron cylinders, diameters between 32 mm and 80 mm and maximum length of 600 mm. The machine is composed of a closed structure with pneumatically opening doors, of a supporting beam of the rotary welding system and of a bearing device to lock and centre the particular to be welded. The machine is arranged to load two couplings.



This is an equipment for welding of corners on cooking plates, maximum dimensions 2400x1000 mm² and maximum welding length of 120 mm. The machine is made up of a supporting bench of the particular, of an inner template and an external device to lock the edges to be welded and of a vertical welding slide including a torch support.



Equipment for induction welding of copper pieces. In this particular case, the equipment is used for joining bundles of tubes which make up a collector for solar panels. The equipment is made up of a number of pneumatic clamps which help hold in position the various components in the collector, and of a controlled axis for step-by-step shifting of both inductors.



This equipment includes a controlled axis lather and is suitable for MIG circumference welding of small spherical caps for the production of steel spherical pieces. Its automatic closure, the centring phase in line with the welding axis as well as the automatic unloading of the welded piece make this compact equipment very easy to use. The whole equipment is enclosed in a stainless steel cell which ensures convenient protection for the user from the glare produced by the welding.



Automatic equipment with lathe for double TIG welding with cold wire of flanges on aluminium tubes, diameters between 300 mm e 660 mm and maximum length of 8000 mm. The unit is composed of a machined beam with two moving heads to adjust the length of the pipe to be welded and complete with two lifters, two expanders to lock and centre the flanges and two motorized vertical slides with torch support to adjust the diameter of the pipe to be welded.



Plasma cutting equipment for iron, stainless steel and copper tubes with diameters between 80 mm and 650 mm, thickness from 0,5 mm to 1 mm and maximum length of 1mt. The unit is composed of a rugged structure, of a clamping mandrel to lock the tube, carrying out the rotation and the translation of the tube and of a vertical slide for the plasma cutting torch. It’s possible to create any kind of figure to import from dxf by suitable software managing the two interpolated axis.



Laser cutting equipment for stainless steel and copper tubes with diameters between 80 mm and 400 mm, thickness from 0,5 mm to 1 mm and maximum length of 2mt. The unit is made up of a closed structure with a clamping mandrel to lock the tube, of two Cartesians axes for the movement of the cutting head and of an automatic unloading of the welded pieces. It’s possible to create any kind of figure to import from dxf by suitable software managing the two interpolated axis.

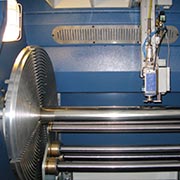